Validation de l’uniformité
d’émission de lumière de 100 à 20 %
Pour valider ce principe, nous avons conduit une série de développements et de tests sur plusieurs points : forme et taille de l’écran, manière d’injecter la lumière, type de peinture, motifs pour obtenir l’homogénéité et manière de peindre, etc. Après une rapide revue de ces axes d’étude, c’est le procédé d’application de la peinture qui est développé dans les paragraphes qui suivent.
Nous avons testé successivement des écrans de forme carrée de 200 mm x 200 mm puis rectangulaire de 200 mm x 600 mm, en utilisant la peinture BC-620 de Saint-Gobain au pinceau. Pour ces écrans, l’injection était réalisée via un guide de lumière en forme de « queue de carpe ». Si 80% de la surface de l’écran avait une émissivité de lumière comprise entre le maximum et max/5, la forme de l’écran en longueur montrait ses limites pour une calibration rapide de tous les PMT. Il fallait alors trouver un écran de dimensions plus grandes. Le troisième prototype d’écran repose sur une autre technologie : l’injection de lumière ne se fait plus via une queue de carpe mais grâce à la courbure de deux fibres optiques entourant un écran circulaire, toujours peint en blanc au pinceau. Avec ses 384 mm de diamètre, cet écran était de taille satisfaisante, mais les résultats expérimentaux d’homogénéité étaient catastrophiques dus à des fuites de lumière. Le quatrième écran remet la queue de carpe au goût du jour, en injectant la lumière sur une tranche d’un écran octogonal. Si l’application de peinture au pinceau est toujours utilisée, elle est comparée avec une application au pistolet à peinture puis au dip-coating. Au-delà de résultats expérimentaux inégalés, la quantité de peinture déposée est connue, les motifs sont simples et la technique est reproductible.
Le contrôle de fabrication pour le dip-coating
La technique du dip-coating est bien connue dans l’industrie pour enduire des pièces unitaires (comme dans notre cas) ou bien des produits continus (rubans, tissus, etc.). Les enductions peuvent concerner des peintures, laques, etc., ou alors des liquides plus spécifiques où des particules chargées sont mises en solutions pour ensuite recouvrir le produit.
Schémas représentants les différentes
étapes d’un dip-coating.
D’après Sol-gel technologies for glass producers and users, J. Puetz & M. A. Aegerter
Dans notre cas, le liquide de recouvrement est un mélange à 80 % de BC-620 de Saint-Gobain et 20 % d’eau déminéralisée. D’autres ratios ont été testés au préalable mais les mélanges s’avéraient trop visqueux et difficiles à manipuler. L’écran, attaché à une motorisation verticale, est alors positionné dans une cuve en aluminium. Cuve et motorisation sont solidaires, rigidement attachées à un socle posé sur une table qui se doit d’amortir les vibrations. Après une homogénéisation énergique du mélange peinture – eau, celui-ci est versé dans la cuve. S’ensuit alors l’étape de remontée, choisie à une vitesse de 2 mm/s. Une fois l’écran totalement émergé, le processus de séchage dure plusieurs heures. Par sécurité, l’écran est décroché de la motorisation 24h plus tard, soit pour être testé au niveau de ses performances optiques, soit pour être à nouveau recouvert d’une couche supplémentaire..
Comparaison avec les techniques précédentes
En effet l’injection de lumière se faisant par une tranche, on souhaite « garder » la lumière proche de l’injection (là où l’intensité est la plus élevée) afin de la distribuer de manière homogène. Ceci passe par une opacité plus importante proche de l’injection. En pratique, cette idée d’avoir un dégradé de peinture était déjà utilisée sur les autres formes d’écrans lorsque la peinture était appliquée au pinceau, mais la quantité à déposer était inconnue, ce qui rendait l’opération artisanale et non-reproductible. Avec le dip-coating, des masques sont réalisés en plaquant un film en polyéthylène, précautionneusement tendu sur les bords de l’écran avec du scotch papier dédié. Ces masques se révèlent parfaitement efficaces, quoiqu’exigeant beaucoup d’attention lors de leur mise en place mais aussi lors de leur retrait, qui est à réaliser avant que la peinture ne soit totalement sèche afin d’éviter qu’elle ne craquelle.
Comparaison avec les techniques précédentes
En effet l’injection de lumière se faisant par une tranche, on souhaite « garder » la lumière proche de l’injection (là où l’intensité est la plus élevée) afin de la distribuer de manière homogène. Ceci passe par une opacité plus importante proche de l’injection. En pratique, cette idée d’avoir un dégradé de peinture était déjà utilisée sur les autres formes d’écrans lorsque la peinture était appliquée au pinceau, mais la quantité à déposer était inconnue, ce qui rendait l’opération artisanale et non-reproductible. Avec le dip-coating, des masques sont réalisés en plaquant un film en polyéthylène, précautionneusement tendu sur les bords de l’écran avec du scotch papier dédié. Ces masques se révèlent parfaitement efficaces, quoiqu’exigeant beaucoup d’attention lors de leur mise en place mais aussi lors de leur retrait, qui est à réaliser avant que la peinture ne soit totalement sèche afin d’éviter qu’elle ne craquelle.
A droite, sont visibles le réservoir avec l’écran vierge à l’intérieur et l’entonnoir prêt à être utilisé, ainsi que la motorisation verticale, le tout attaché à un socle. On aperçoit au second plan les pots de peinture et le générateur de tension pour le moteur.
A gauche : masque en polyéthylène, maintenu sur l’écran grâce à du scotch papier.
Perspectives d’amélioration :
vers l’automatisation
Dispositif de dip coating avec panneau en trempageEn l’état, ce banc de production est loin d’être définitif. Plusieurs axes de recherche sont à étudier pour comprendre plus finement le processus d’enduction, en particulier l’impact de certains paramètres sur l’épaisseur de peinture : température de la pièce, taux de dilution (et donc densité, viscosité et tension de surface du liquide), vitesse de remontée, état de surface de l’écran, etc. De plus par faute de commercialisation, la peinture de Saint-Gobain sera remplacée par une peinture similaire (EJ-510 de Eljen). Cette caractérisation pourrait se traduire par l’ajustement de formules ou d’abaques issues de la littérature, utilisables ensuite pour optimiser la couverture de l’écran de calibration voire même dans d’autres conceptions de détecteurs. Une automatisation de ce banc de production est aussi envisagée, de manière à rendre plus simple son utilisation.
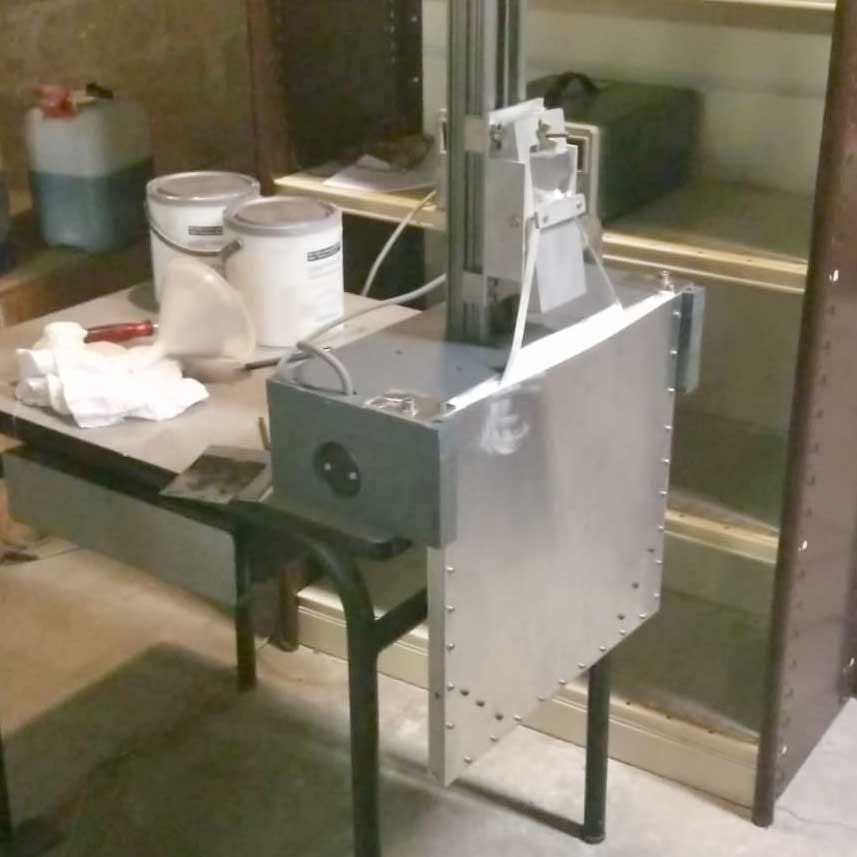
Dispositif de dip coating avec panneau en trempage
Les auteurs remercient la collaboration fructueuse avec leurs collègues du consortium CTA, en particulier pour les projets MST et NectarCAM. Ce projet a bénéficié du soutien du LabEx P2IO (contrat ANR-10-LABX-0038) dans le cadre du contrat “Investissements d’Avenir” ANR-11-IDEX-0003–01 de l’Agence Nationale de la Recherche (ANR, France).